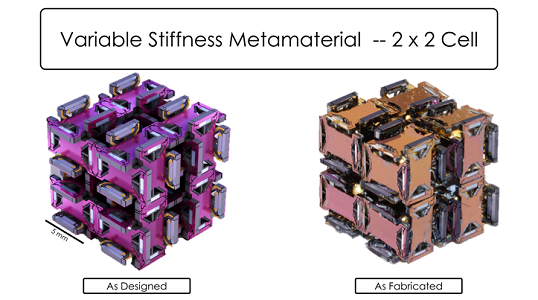
One new project in the NDML is the design, fabrication, and assembly of novel MEMS devices to create mechanical metamaterials with programmable stiffnesses. The MEMS devices used in this project are designed to have unique bidirectional thermal actuators which are capable of outputting large amounts of force in both tension and compression. The bidirectional MEMS actuators contain two actuating components, the inner actuator and outer actuator, both contained within an out-most enclosure. The outer actuator consists of a pair of multi-chevron beam structures mirrored and connected at the anchor and the inner actuator is a set of horizontal beams connecting the anchors through the handle layer. When a voltage is applied across the black electrodes, current flows through the outer actuator and the chevron beams undergo joule heating and thermal expansion. The outward horizontal motion at the anchors are restricted by the inner actuator beams, resulting in an upwards displacement at the tip of the device. Conversely, when a voltage is applied across the white electrodes, current flows through the center beams. The thermally expanded beams push the anchors outwards which results in a downwards displacement at the tip of the device. The MEMS devices also have piezoresistive strain sensors which are capable of very sensitive displacement measurements. Therefore, when the MEMS devices are assembled into a cube, they are capable of measuring an input force applied to the cube and then outputting an equal but opposite force to the MEMS device resulting in zero net displacement of the cube. Because the MEMS devices are optimized to output very high forces per unit area, the assembled cubes are capable of maintaining an infinite effective stiffness over a wide range of applied forces. This type of programmable stiffness allows the assembled metamaterial to achieve real-time control over its elastic properties which is critical in a number of military and aerospace applications.